The ash from burning coal in coal-fired power stations lies in thousands of landfills around the world. This waste material, generally considered a hazard, is now being put to good use in the construction industry.
More than 6,000 coal-fired power stations produce this powdery byproduct, which is properly known as “pulverised fuel ash” (PFA) or “fly ash”. Traditionally, it was released into the atmosphere from the smoke stack after the coal was burned, but, because of its effect on air quality, it is now captured and stored in landfills.
Our research focuses on how we can recycle and make best use of these types of dirty byproducts for the sake of the environment.
alegga/Shutterstock
The current demand for concrete worldwide is around 14 billion cubic metres annually. This is projected to increase by 43% to 20 billion cubic metres by 2050. The impact of the carbon dioxide emissions (8% globally) that is associated with this increase, against the backdrop of the current environmental crisis, is immense.
There is a dire need for a change in lifestyle and for tighter environmental regulation of industrial operations and processes. This should include a serious mitigation of the worsening environmental landscape. Increasing the use of industrial waste and byproduct materials is one such strategy.
Some of the most abundant global waste streams result from the many years of coal mining, so the role that can be played by re-using coal waste, including PFA, is significant.
And this idea is based on old technology if you consider how the Romans used ash. The dome of the Pantheon in Rome, built in AD128, as well as the Colosseum, are examples of successful structures built with volcanic ash-based concrete.
Portland cement
PFA can be blended with Portland cement to make concrete. That’s the most common type of cement in general use around the world and is a basic ingredient of concrete, but also mortar, stucco and some grout. Portland cement is a hydraulic cement, which means that it reacts with water to form a paste that binds sand and rock together, creating concrete. Around 3.5 billion tonnes of Portland cement are produced annually.
The problem, though, is that producing Portland cement uses a lot of energy and also precious natural resources. You must quarry the raw materials, which not only damages the landscape but also results in emissions of up to 622kg of carbon dioxide per tonne of cement.
Lessening the impact of Portland cement on the environment is therefore vital. PFA is the most attractive byproduct for this purpose, due to its abundance and low cost. Also, if it is properly used in combination with Portland cement, it can result in stronger and more durable concrete.
However, as more coal-fired power stations are decommissioned and fewer come into operation worldwide, stockpiles of PFA become depleted. This means we will need to use the material more efficiently in the future.
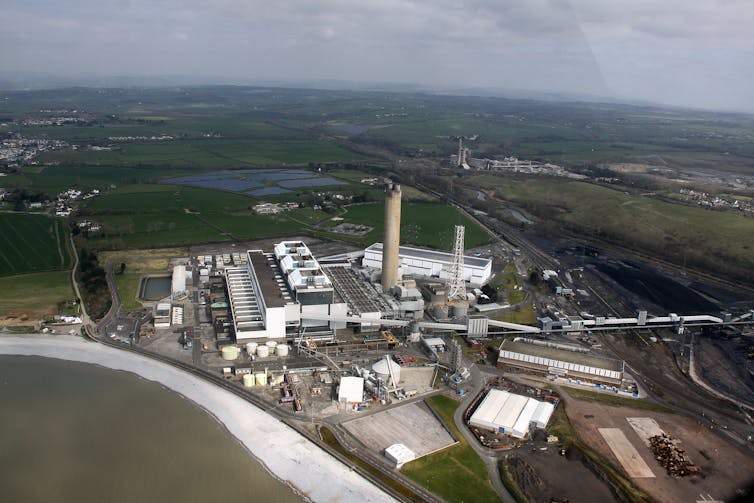
Ben Salter/Flickr, CC BY
Attention will have to shift to different types of fly ash or unburnt colliery waste. But coal mining waste, either from current or past mining activities, will continue to feature in the construction industry for a long time.
And besides concrete, there are also other ways in which we can recycle PFA. This includes using it to improve the properties of soils, making abrasives such as sandpaper and grinding wheels, and using it in the manufacturing of a variety of products, such as plastics, paints and rubber.